Bryan Builders is a family-owned General Contracting firm that specializes in the industrial, commercial and e-commerce industries throughout the U.S.
As a dedicated team of construction professionals, we bring over 400 years of combined experience to the table for our clients. We believe in establishing a culture that operates on integrity and always putting the client’s needs first. Our team strives to create relationships with our partners that are built upon trust, respect, and honesty. Here at Bryan Builders, we can show you a new level of dedicated service and the highest standards of quality and safety!
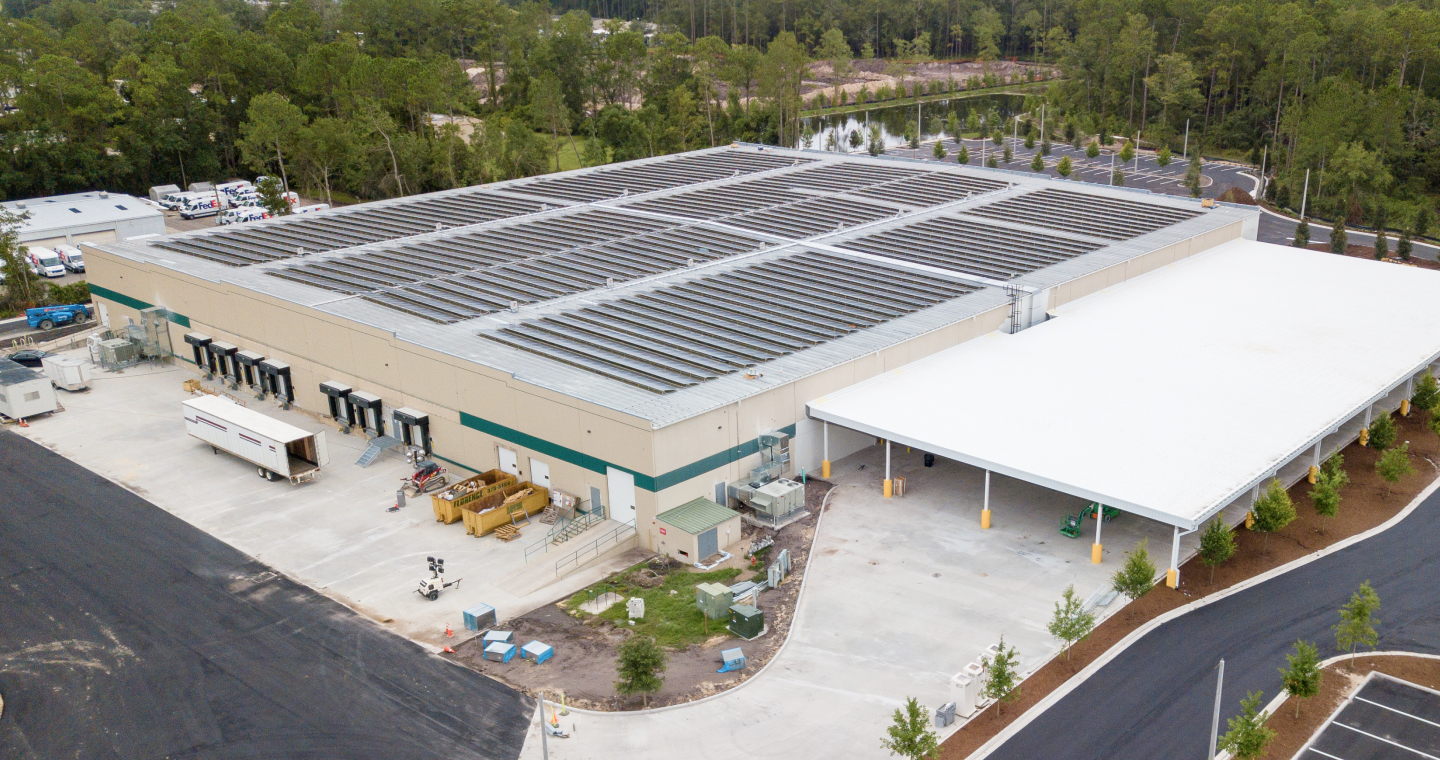
Our History
Founding member, Scott A. Bryan, launched Bryan Builders, LLC in 2010 with the purpose of creating a lasting culture that was based upon truly serving each client, partner, and team member and always operating with integrity. Over time, this belief in a strong culture has helped us to evolve into an established team with over 400 years of combined experience! Scott, along with his invaluable teammates and partners are focused on maintaining the strong values that this company has been built upon and consistently giving each client unmatched service.
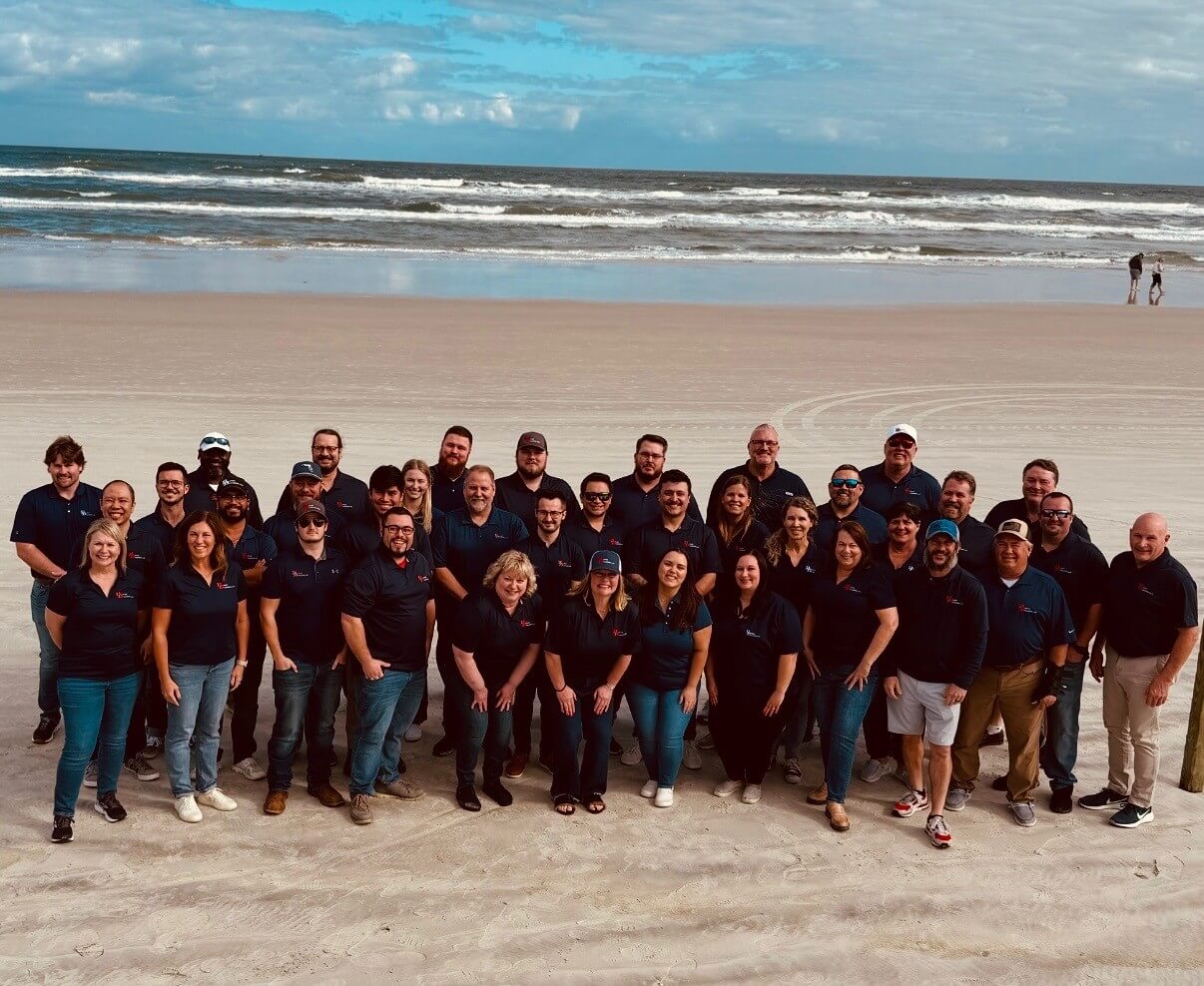
Experience
The team at Bryan Builders is a dynamic group of highly experienced construction professionals.
Each member brings a wealth of knowledge in all different construction markets. With over 400 years of combined experience, Bryan Builders can be your expert in: Commercial, Industrial, Logistics, E-Commerce, Retail, Tenant Upfit, Sitework, and Design Build. We Pride ourselves on making the process turnkey for all our clients and deliver nothing but the best in quality and reliability.
Let the Bryan Builders team show you our superior service and dedication on your next project!
Leadership Team
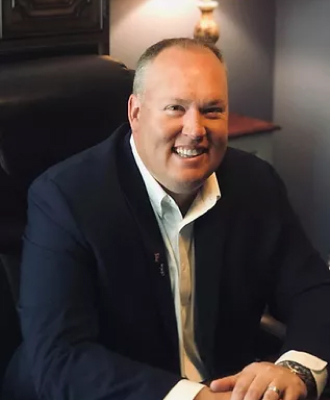
Scott A. Bryan

Stephenie Bryan

Martin Foster
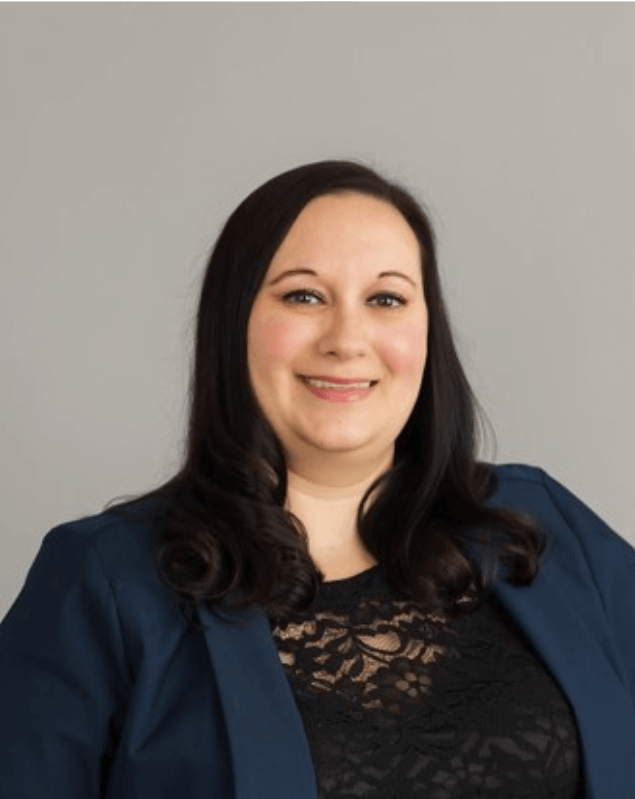
Jessy Bezemek
Director of Construction Adminstration

Chuck Pruett
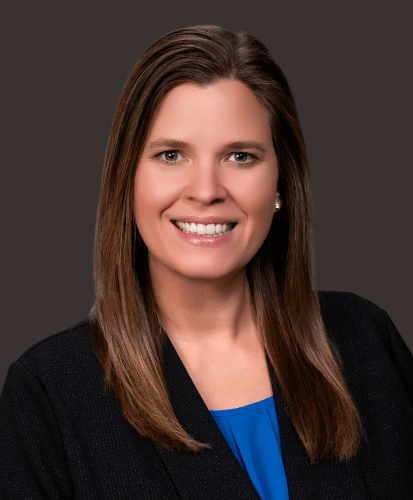
Jen Pruett
Operations Coordinator
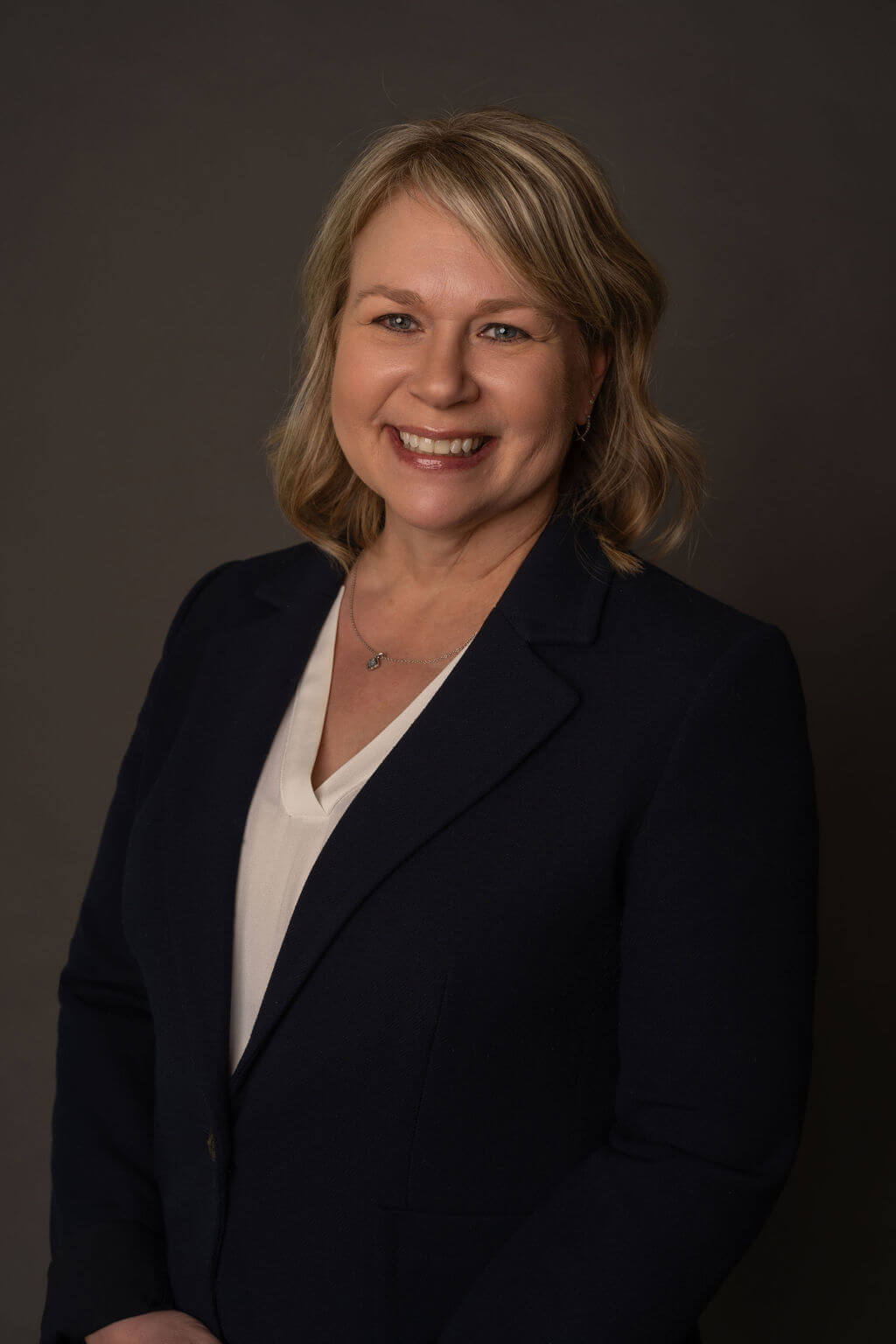
Tracy Williams-Prince
Executive Director
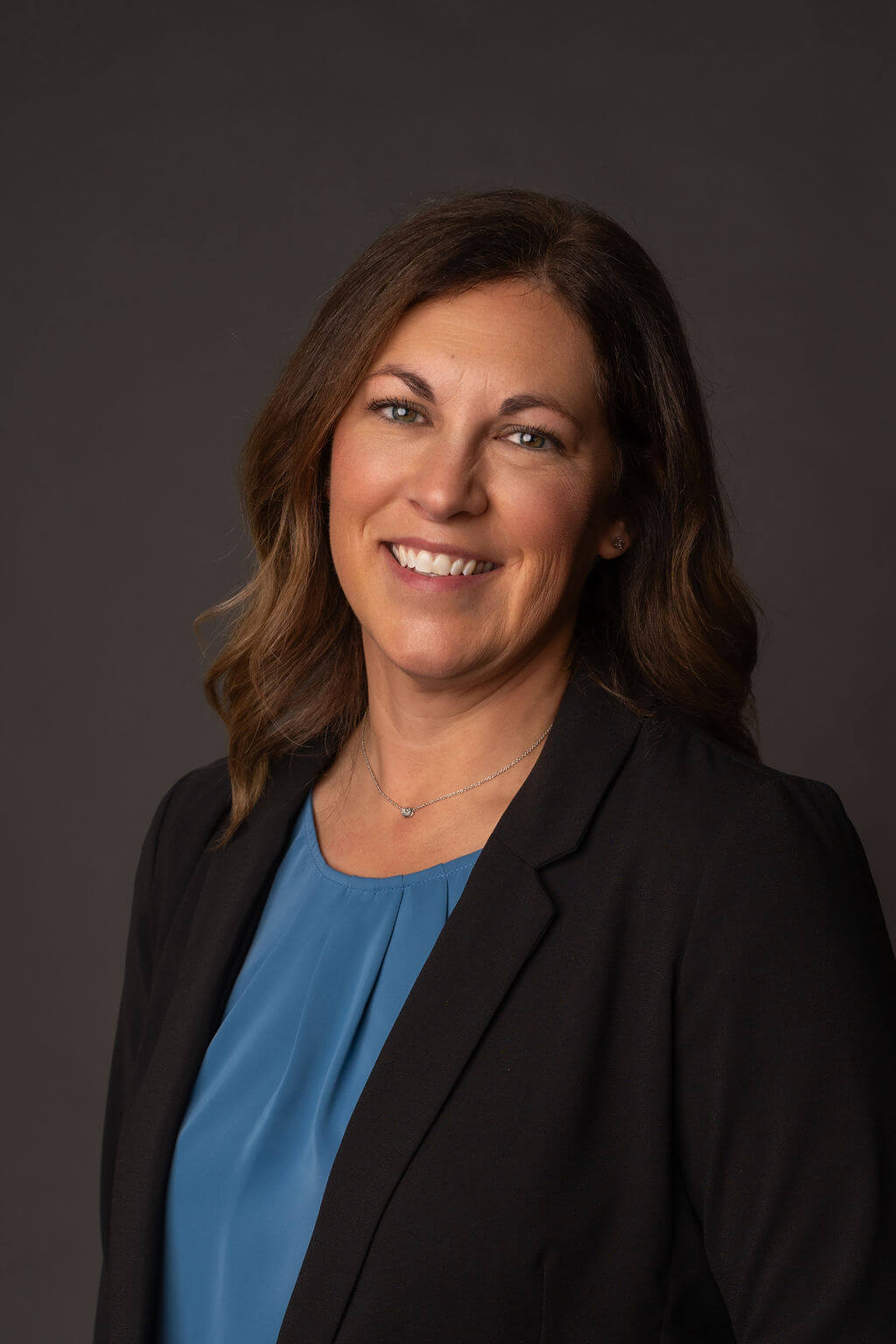
Tami Bloedorn
Director of Accounting
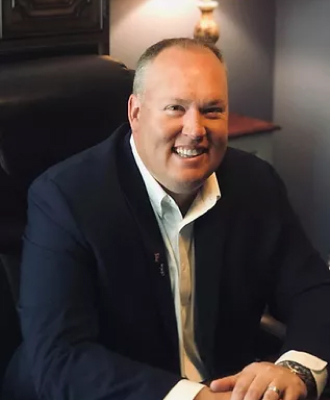
Scott A. Bryan
As President and Principal of Bryan Builders, LLC., Scott has more than 20 years of experience in the construction and design build industry. After graduating from the M.E. Rinker College of Design, Construction, and Planning at the University of Florida, he worked on over 100 commercial, office and retail projects with J. Raymond Construction Corp.
While there, he grew his career rapidly from a Field Engineer, to Super, PM, and Sr. Project Manager and established his reputation by successfully completing numerous projects for companies such as Publix, Wal-Mart, Fresh Market, Aldi and as well as numerous private developers. Scott soon moved on to take a position with DDC, a full-service design-build general contractor, as their Vice President of all construction related activities. There, he led a large team throughout the U.S. and Canada, building a wide range of projects from CNG fueling stations to projects for Wal-Mart and Amazon & Med-Express.
Scott knew that in forming Bryan Builders, he would be able to combine all his industry knowledge, relationships and customer service into an organization that would not only be successful, but also serve his clients to the fullest. These qualities have brought Bryan Builders continued success with several high profile negotiated clients.
Scott’s values of always putting the customers and employees first has helped him build a first class team and positioned Bryan Builders for significant growth and strong partnerships in the future.

Stephenie Bryan
After many years in the oil, gas and energy markets, Stephenie Bryan joined the Bryan Builders team as Director of Business Development and Marketing. Over the last 15 years, she has worked her way from Business Development Manager up to VP of Sales, leading many different sales organizations to achieve growth year over year.
As Stephenie’s talents in this industry grew, she accepted a role as Director of Sales for a new division within U.S. Venture, GAIN Clean Fuel. There, she grew a network of Compressed Natural Gas fueling stations for class 8 trucks from 3 sites to 52 sites, throughout the US and Canada, in a time span of 3 years. With a very diverse customer base, Stephenie built CNG fueling stations for Anheuser-Busch, Lowes, Ryder and several other national trucking and logistics companies, under 5-10 year fueling contracts.
Through the process and completion of these projects, she learned a great deal about construction management and many other operational skills that will be significant in her role with Bryan Builders.
Stephenie has always believed in building strong relationships with customers, her team and business partners throughout her career and she will continue to drive this within Bryan Builders. Her dedication to the success and growth of the business will be one of the key attributes in the continued progress of the company and team.

Martin Foster
As a true construction management professional in the industry, Martin has over 27 years of experience with many high-profile projects, including numerous ground up, site work, and tenant buildouts. His proactive nature, organizational skills and understanding of the client’s needs and expectations is remarkable, and makes him a valuable asset to the Bryan Builders organization.
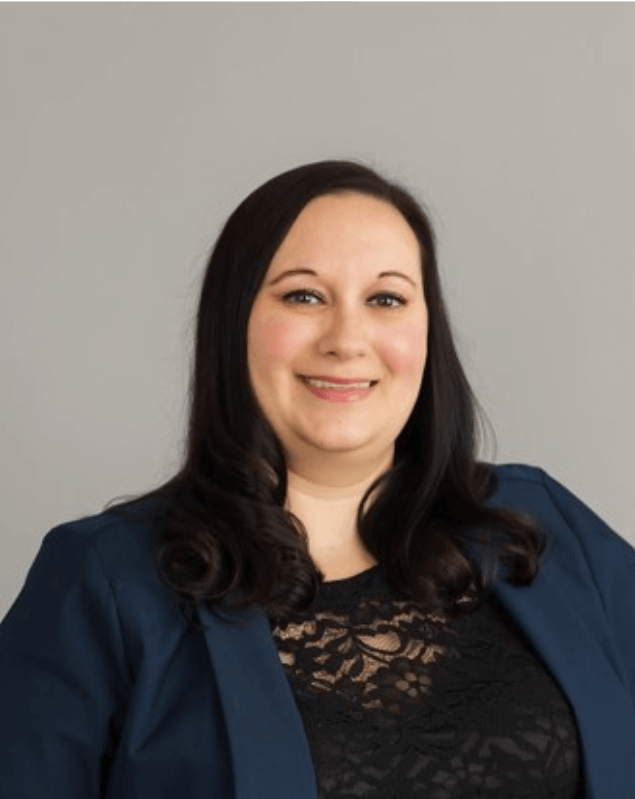
Jessy Bezemek
With nearly a decade of experience in commercial construction and a foundation in residential building, Jessy brings a deep understanding of the industry and a clear vision for its future. After starting her career, she joined Bryan Builders where she has grown from Construction Administrator to Director of Construction Administration. Along the way, she played a pivotal role in building Bryan Builder’s standard operating procedures and has been instrumental in shaping the company’s evolving tech landscape. Jessy is known for her attention to detail, organizational strength, and analytical approach to problem-solving. She’s deeply committed to the growth and development of her team, continually fostering a culture of collaboration and excellence. Her leadership continues to be a driving force behind Bryan Builder’s progress, with a focus on building lasting relationships and elevating the success of both the business and its people.

Chuck Pruett
Chuck has 20 years of experience as a safety professional in the construction, environmental health, and insurance industry. He was, most recently, at Keller, the world’s largest geotechnical specialist contractor, where he managed safety and risk for many high profile projects throughout the US and Canada. In his role as Director of Risk Management and Safety at Bryan Builders, Chuck is responsible for ensuring the safety and security of all the people, assets, and processes across the organization.
Chuck is actively involved in promoting safety in the industry. He is a member of the American Society of Safety Engineers (ASSE). Chuck holds a Bachelor of Science in Occupational Safety and Health from Illinois State University, is a Certified Safety Professional (CSP) and Construction Health and Safety Technician (CHST), and also obtained the Construction Risk and Insurance Specialist (CRIS) certification.
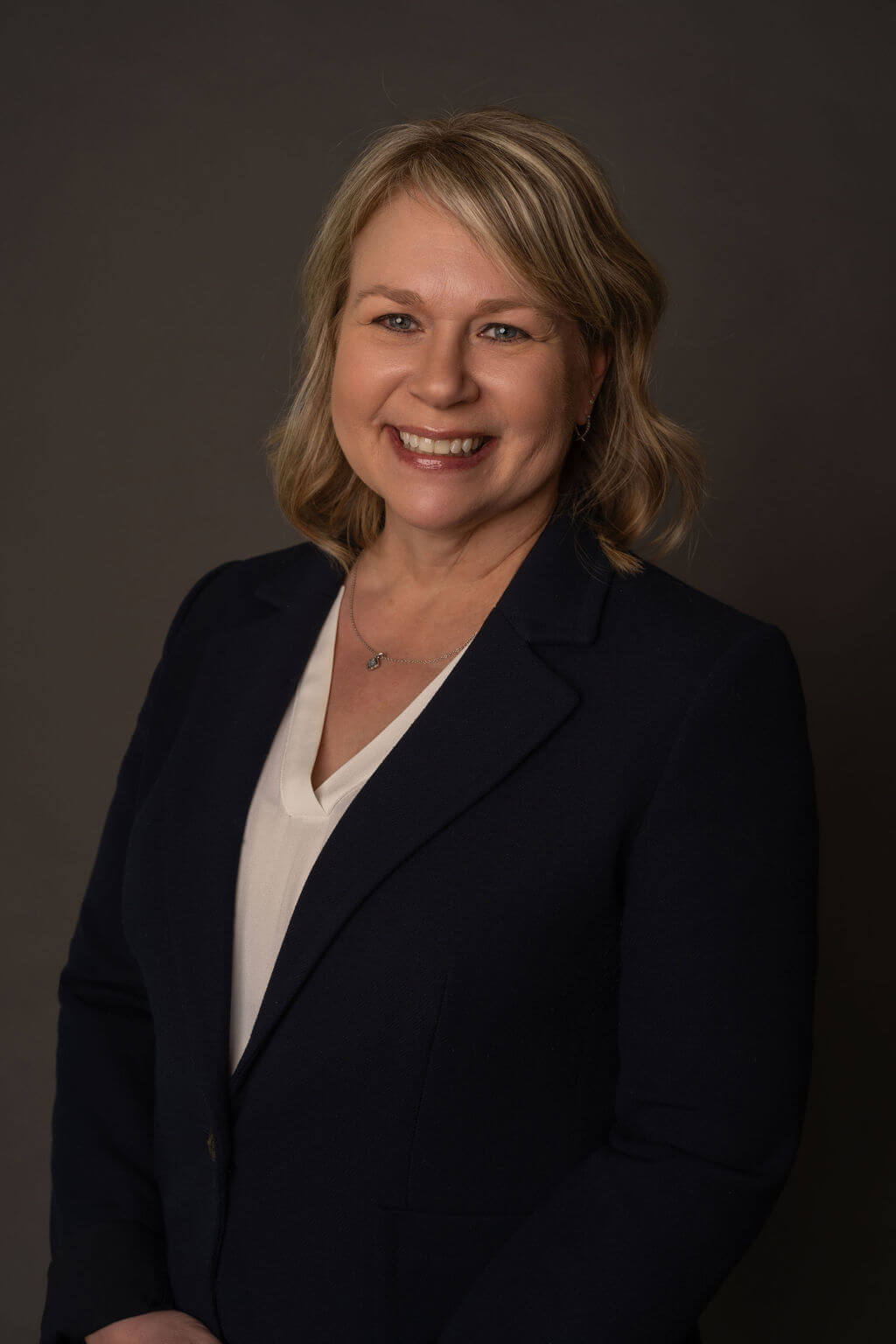
Tracy William-Prince
Tracy Williams-Prince brings a long background in marketing, business development, and human resources to her role as Executive Director at Bryan Builders. She is passionate about driving organizational growth, developing strategic initiatives, and executing results-driven campaigns. Tracy plays a key role in marketing, business development, and human resource management, ensuring seamless day-to-day operations while identifying new opportunities for expansion.
With a keen eye for market analysis and a talent for blending creative innovation with data-driven insights, Tracy excels at uncovering growth opportunities and crafting comprehensive strategies that move businesses forward.
Tracy holds a journalism degree from the University of Wisconsin–Eau Claire and a Master of Business Administration from Concordia University. Outside of work, she enjoys being active outdoors during Wisconsin’s beautiful summers and cheering on the Green Bay Packers during the chilly winter months.
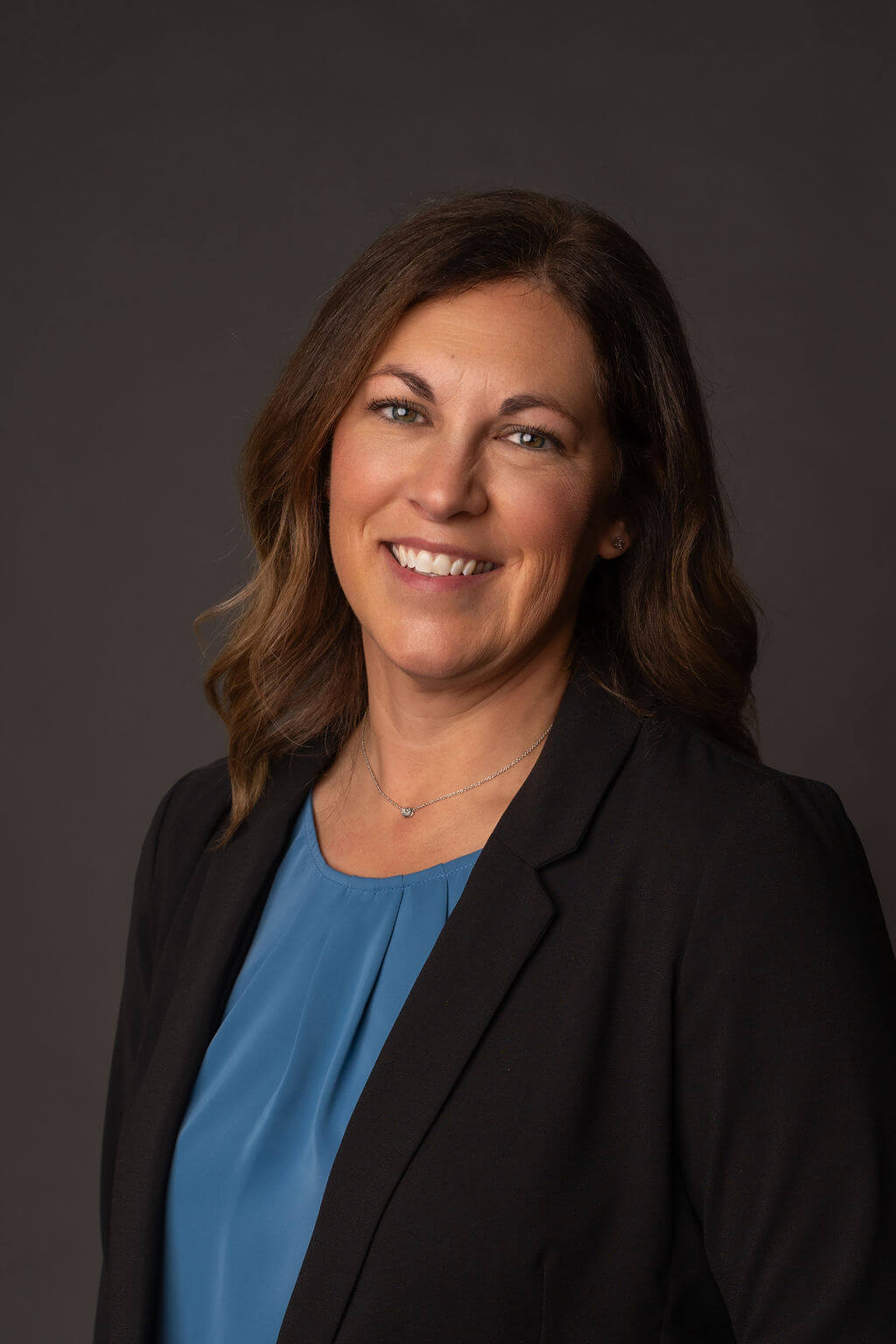
Tami Bloedorn
With more than 15 years of experience in the construction industry, Tami joined Bryan Builders bringing expertise in accounting, human resources, benefits management, and finance. With dual bachelor’s degrees from the University of Wisconsin – Oshkosh in Accounting and Finance, Tami brings a unique background of fiscal management along with talent management that she hopes will help Bryan Builders grow to the next level. Working in firms both large and small, Tami’s breadth of experience will be used to create processes and procedures needed for this fast-paced and quick-growing company. As Director of Accounting, she will be responsible for directing the accounting operations of Bryan Builders and hopes to help build the foundation for increased growth.
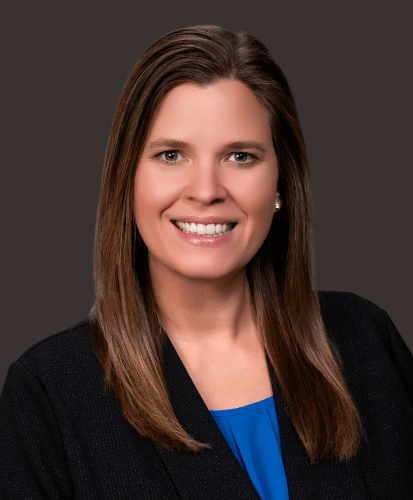
Jen Pruett
Jen Pruett is the kind of person who keeps everything running smoothly behind the scenes. With a strong background in operations, team leadership, and process improvement, she’s always looking for ways to make things more efficient and effective. She first joined Bryan Builders as a Preconstruction Administrator but quickly transitioned into her current role as Operations Coordinator, where she helps streamline workflows, optimize resources, and keeps day-to-day operations on track.
Before Bryan Builders, Jen worked as a Customer Experience Supervisor, leading a team that supported high-value clients and improved service operations. She has a knack for enhancing processes, bringing teams together, and finding practical solutions, making her a key part of the Bryan Builders family.
Jen is all about building strong relationships and making work easier for everyone. With her knowledge in customer experience, project coordination, and cross-functional teamwork, she brings fresh ideas and a collaborative approach to every challenge.
She holds a Master’s degree in Business Administration and is passionate about continuous improvement, problem-solving, and creating a positive work environment.
When she’s not at work, you can find Jen traveling with her family, baking with her daughter, watching her kids’ sporting events, or soaking up every bit of the Midwest summer sunshine.
Project Management

Kevin Banks
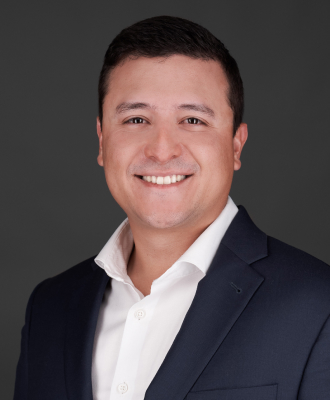
Ricardo Madero

Noah Burnett
Project Manager
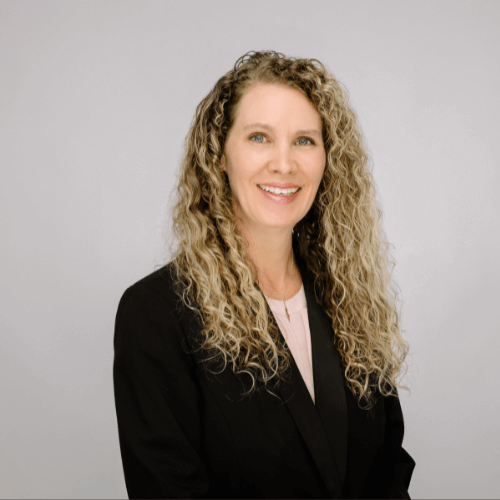
Sherri Bahns
Project Manager
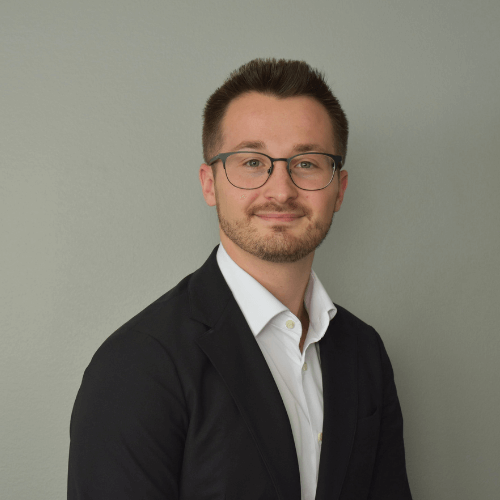
Bailey Dillon
Assistant Project Manager

Kevin Banks
Kevin came to Bryan Builders with over 30 years of construction experience in various disciplines from heavy civil and marine to military, commercial and industrial. Kevin can take any project from conception, through design and execution no matter the size or scope of the project. Kevin is a strong leader who has worked throughout the US with clients of all types and sizes and always values the relationships built and successes obtained. Kevin will always put honesty and integrity of himself and his team first in building strong partnerships while serving the client.
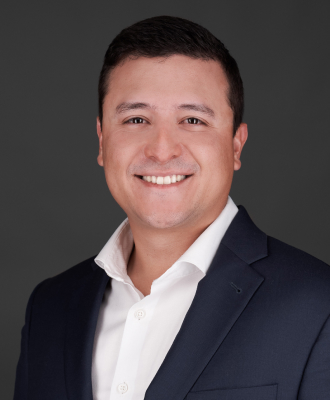
Ricardo Madero
Ricardo has been with the company for a few years and in that time has quickly proven his ability to manage high level projects throughout the United States. Ricardo started as a Field Engineer, was quickly promoted to Assistant PM and now as Project Manager oversees multiple sites. He comes from a Military background with 4 years of service in the U.S. Navy and obtained his BS in Construction Management from the University of Florida. He’s managed some of the largest and most complex projects in the company’s history and has extensive experience working on active sites. His attitude and work ethic help drive these projects to the finish line all while building lasting relationships with our clients and trade partners.